An Actual Solution to the Plastic Pandemic from Innovative Canadian Startup Polystyvert
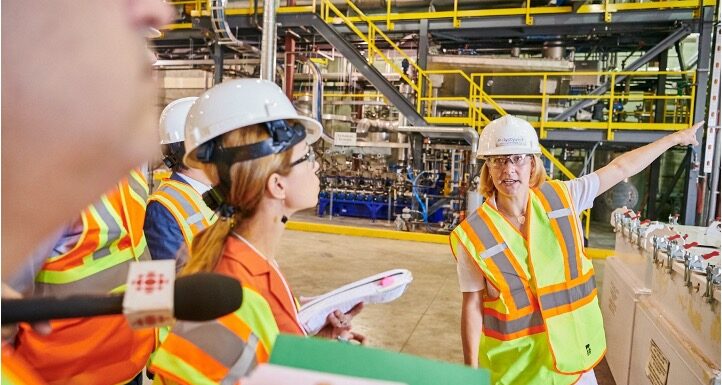
There is a wide range of styrene-based products manufactured globally. There are 26 million tons of polystyrene, and 11 million tons of ABS produced every year – most of it eventually ending up in landfills or the ocean. Polystyrene is used to insulate buildings, reinforce bicycle helmets, or produce yoghurt containers. ABS is another styrene-based plastic used in cell phone casings, automotive parts, and toys, among other things.
Many plastics are not recycled today because they are too contaminated. They are often mixed with other plastics, tape, paper, cardboard, or metals, and can also contain additives such as flame retardants that make the recycling process very challenging. And until now, styrene based products have been notoriously difficult to process at scale.
Polystyvert has developed an innovative technology to recycle styrene-based plastics in a closed loop. Using a patented dissolution technology, it has developed an innovative process to remove contaminants. Making styrene plastics liquid allows the application of advanced purification methods, resulting in a very high-quality recycled plastic.
The first and most important step is the purification process. The polystyrene is quickly dissolved in an essential oil (p-cymene) just like sugar in a cup of coffee. Since other plastics do not dissolve in the solvent, it is a very safe and efficient way to remove contaminants by simple coarse filtration.
Polystyvert then applies its proprietary purification process. This is a flocculation process that removes all contaminants in suspension (graphite, pigment, other additives, etc.). After this purification, the polystyrene is perfectly transparent, but is still liquid.
The next step is precipitation to make the polystyrene solid. Another solvent is added to the liquid polystyrene causing it to precipitate. At this stage soluble contaminants such as HBCD or certain dyes are separated from the polymer and remain in the solvent.
Finally, a polystyrene paste is obtained which is then devolatilized to obtain pellets. All the steps (except for the extrusion) are carried out at low temperatures, which allows all the mechanical properties of the polystyrene to be retained. The molar mass and MFI of the output are the same as those of the input. The resulting PS is of high quality and purity, with a yield of over 95%.
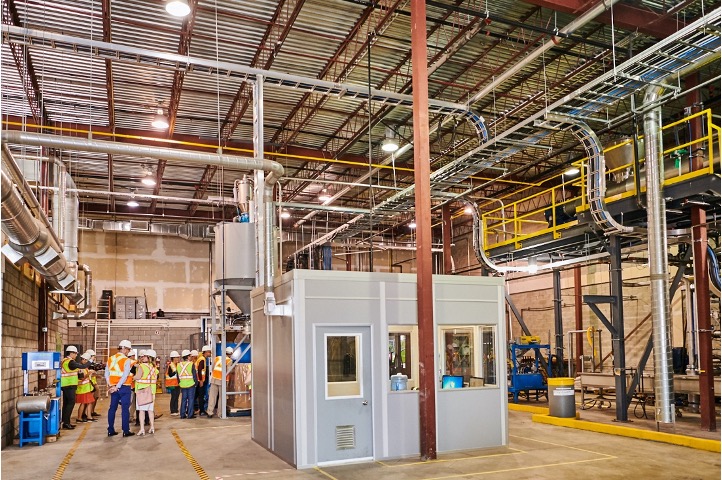
By recycling plastic waste that would normally be doomed to landfills, Polystyvert has created a clean technology that allows the world to continue to benefit from the vast applications of polystyrene without relying on the oil and gas industry.
Several life-cycle analyses have been carried out and show that Polystyvert’s proprietary technology reduces GHG emissions by over 75% compared to the production of virgin polystyrene. This demonstrates the major impact of employing a circular economy for styrene-based plastics and the resulting environmental protection.
To protect its invention, Polystyvert has filed several patents regarding its dissolution and purification processes in Canada as well as around the world. The protection of intellectual property is a top priority for the company.
Polystyvert has obtained a letter of certification for recycling food packaging in the U.S. This creates a tremendous business opportunity for manufacturers who package food products made from polystyrene such as coolers, which are used to transport fish and seafood at a stable temperature. These coolers are also used to transport vaccines.
Polystyvert was founded in 2011 by Solenne Brouard Gaillot. In 2012 the start-up received financial support from the SDTC and Recyc-Québec agencies. Shortly after Angel and private investors became interested. The team was quickly strengthened with the additions of Professor Roland Côté who took over the management of the R&D department and Marianne Lépinoit who was the cornerstone of successive rounds of fundraising, all important for start-ups. Polystyvert filed its first patents in 2014 and in 2015 started its first pilot line in Anjou, Quebec.
In successive rounds of funding, leading investors such as Cycle Capital Management, Anges Quebec, Energy Foundry and Quadriam have enabled Polystyvert to raise sufficient capital to scale its technology. In 2018, its demonstration plant was launched operating at 125 kg/h. Recently, Polystyvert closed a new round of funding with strategic investors such as Scandinavian polystyrene producer BEWi and the BDC. The purpose of this round is to facilitate the construction of a full-scale commercial plant in Montreal. This will showcase Polystyvert’s technology and will be operational by 2023.
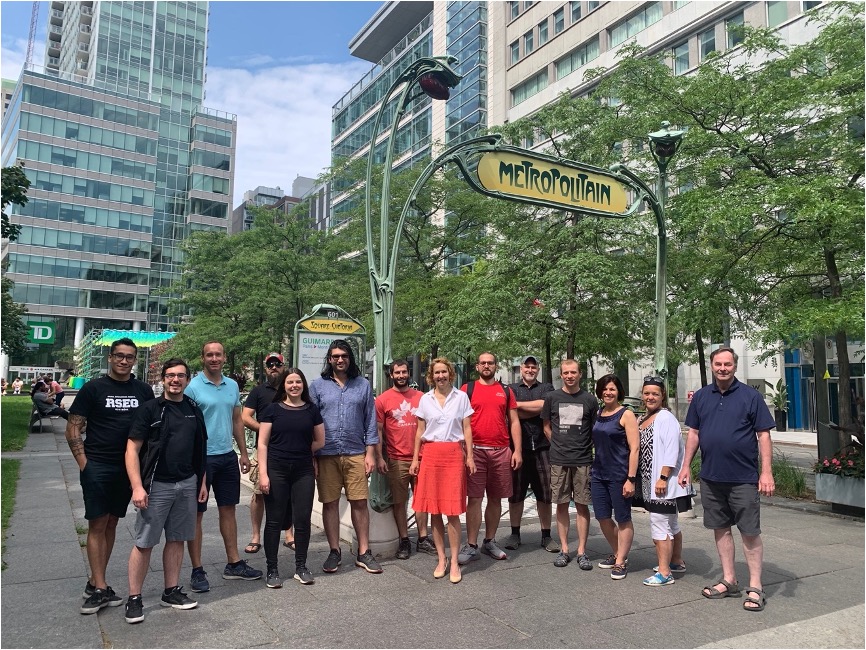
We believe that everyone, and Canadians in particular, should be able to access environmentally friendly products. They can now trust in Polystyvert’s clean technology which allows manufacturers to produce plastic products that are both high performance and good for the planet.