Breaking the Bottleneck: How Smarter Hydrogen Storage and Transport Will Power the Clean Energy Transition
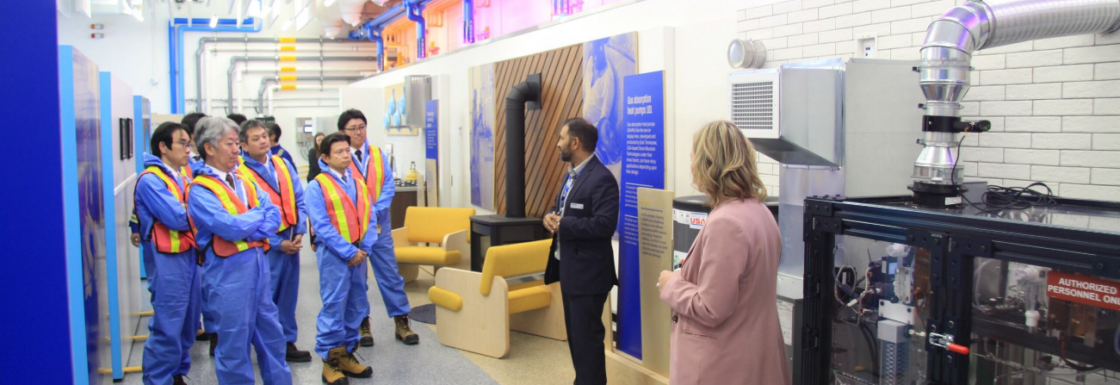
Hydrogen is a rising force in the clean energy transition—versatile, emissions-free, and crucial for decarbonizing heavy industry and transport. But as Dr. Brandy Kinkead of Ayrton Energy highlights, a major challenge remains: cost-effective storage and transport. These often-overlooked hurdles account for up to 70% of hydrogen’s total cost and threaten to stall progress. Unlocking hydrogen’s full potential depends on infrastructure-compatible solutions that can safely, efficiently, and affordably move hydrogen from where it’s produced to where it’s most needed.
As the global energy landscape pivots toward low-carbon solutions, hydrogen is emerging as a cornerstone of future energy systems. With a projected market value of $1.4 trillion by 2050 and Canada targeting 30% hydrogen adoption in its national energy mix, hydrogen’s appeal is clear: it’s clean, versatile, and energy- rich. But despite major progress in hydrogen production and end-use applications, the industry faces a critical bottleneck—cost-effective storage and transportation.
At Ayrton Energy, we believe that solving this challenge is essential to unlock the full potential of hydrogen, especially for hard-to-decarbonize sectors like heavy industry, aviation, marine transport, and long-haul trucking. Our innovative approach to hydrogen storage offers a safer, more efficient, and infrastructure-compatible solution to a long-standing problem.
The Hidden Cost: Storage and Transport as the Industry’s Largest Expense
While attention often centers on how hydrogen is produced—whether by electrolysis, reforming, or pyrolysis—the reality is that up to 70% of hydrogen’s total cost lies in storage and transport. This is not merely a technical inconvenience; it’s a market-limiting factor. Most hydrogen today is used close to where it’s produced because moving it is expensive, inefficient, and risky. Without scalable solutions for storing and transporting hydrogen safely and affordably, broader market adoption will stall—regardless of advances in green production.
The Energy Density Dilemma
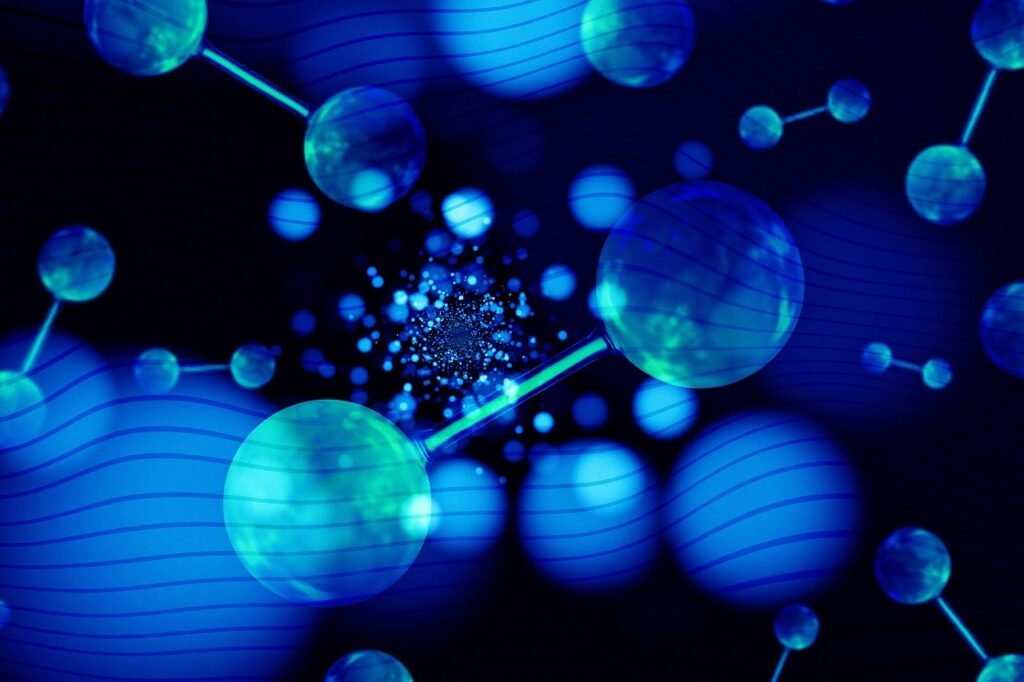
At the core of the challenge lies hydrogen’s physical nature. On a mass basis, hydrogen contains nearly three times the energy of diesel—33.3 kWh/kg compared to 12 kWh/kg. But, but the advantage disappears when considering volume. Hydrogen’s volumetric energy density is less than 1 kWh/l at standard conditions, while diesel boasts 9 kWh/l. That means you’d need greater than ten times more volume of hydrogen than diesel at standard conditions to do the same amount of work—unless you densify it.
Unfortunately, boosting hydrogen’s density introduces tradeoffs in safety, cost, and energy efficiency. High-pressure tanks and cryogenic liquefaction (-253°C) both raise storage costs significantly and create major engineering and safety challenges.
Regarding Safety
Hydrogen’s flammability over a wide range of concentrations and temperatures leads to significant safety challenges. The self-heating of hydrogen during expansion (e.g. moving from higher to lower pressures) and the invisibility of hydrogen flames add further complications.
Regarding Cost and Energy Efficiency
Hydrogen’s small molecular size and reactivity leads to material embrittlement in standard tanks and pipelines, severely limiting the use of existing infrastructures. Moreover, the energy costs for storage can be as high as 80% of the energy that can be derived from the stored hydrogen (round-trip energy efficiency as low as 20%).
Rethinking the Storage Paradigm
Current solutions for hydrogen storage fall into two categories:
- Physical methods, such as compression and liquefaction, which requires specialized tanks and insulation, and have low round-trip hydrogen energy efficiencies (as low as 25%).
- Material-based methods, including solid-state absorption and liquid carriers, offer better hydrogen storage densities and safety profiles—but often face issues with cost, complexity, energy use and compatibility with existing infrastructure.
Our work at Ayrton Energy offers a breakthrough in the liquid organic hydrogen carrier (LOHC) category. Unlike high-pressure or cryogenic methods, our technology uses an electrically driven reactor that stores and releases hydrogen at near-ambient temperatures (<100°C) and pressures. The hydrogen is chemically bound to a carrier oil, creating a dense, stable, and low-toxicity fluid that can be transported using existing oil and gas liquid fuel infrastructure—including pipelines, rail, and tanker trucks. By enabling hydrogen to be stored in this stable liquid form, Ayrton’s e-LOHCTM system decouples hydrogen production from its point of use. This allows clean hydrogen to be generated wherever hydrogen is abundant and low cost —and transported efficiently to where it’s most needed, whether that’s an industrial facility, refueling depot, or export terminal.
This flexibility of our solution supports a scalable hydrogen economy in Canada—especially in Alberta, where we are headquartered and 80% of the country’s hydrogen is produced. With existing infrastructure and export potential to Asia and Europe, Alberta is well-positioned to lead in low-carbon hydrogen. Ayrton Energy’s mission is to enable this growth, driving clean-tech investment, job creation, and global energy diversification.
Performance Without Compromise
Our e-LOHCTM system solves the energy density tradeoff by enabling storage density comparable to cryogenic liquid hydrogen but without the extreme cooling requirements or specialized equipment. And it does so with a roundtrip energy efficiency of up to 80%, significantly outperforming many other carrier systems that hover around 30–40%.
Critically, the dehydrogenation process in our system delivers high-purity hydrogen, eliminating the need for costly purification steps downstream—a major advantage for applications like fuel cells, where impurities can degrade performance such as industrial feedstock applications. Furthermore, our hydrogenation and dehydrogenation processes facilitate easy integration with a small footprint design and compatibility with intermittent operations.
– Dr. Brandy Kinkead
From a company’s perspective, these benefits translate directly to reduced capital expenditure, lower operating costs, and faster deployment timelines. By leveraging infrastructure that already exists, Ayrton’s solution sidesteps one of the most expensive hurdles in hydrogen logistics: building a parallel transport system from scratch.
Enabling Decarbonization in Heavy Industry
Hydrogen is one of the few viable options to decarbonize energy-intensive sectors such as steelmaking, cement, ammonia production, aviation, and shipping. These sectors require fuels with high energy density, fast response times, and minimal emissions—criteria that hydrogen meets in theory, but not in practice unless it can be stored and moved efficiently.
By enabling hydrogen to be stored and transported safely at lower cost and with higher efficiency, our incomparable technology directly supports the expansion of hydrogen into these critical applications. And because the system avoids greenhouse gas (GHG) emissions during the hydrogen release process—unlike some competing technologies that emit carbon dioxide or nitrogen oxides—Ayrton’s solution aligns closely with ESG goals and emerging regulatory standards.
Charting the Path Forward
To make hydrogen a cornerstone of the energy transition, the industry must solve the storage and transport challenges. This is not just a technical requirement—it is the key to unlocking hydrogen’s economic viability and global scalability.
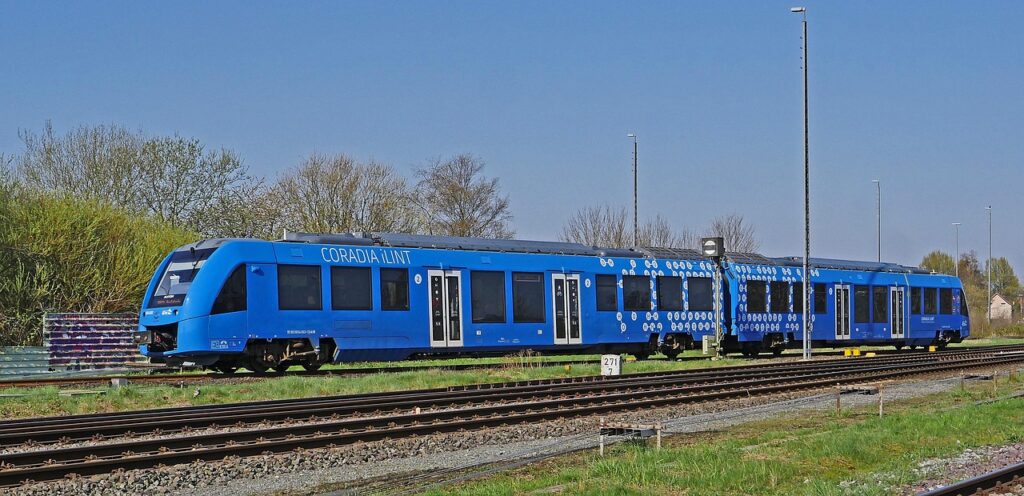
Unlike ammonia-based carriers, which are toxic and costly to insure, Ayrton’s e-LOHC is a safe, low toxicity alternative that simplifies transportation. Rail and shipping companies are increasingly reluctant to handle ammonia due to safety risks and high insurance premiums. Ayrton’s stable liquid carrier avoids these barriers, enabling easier permitting, lower logistics costs, and broader adoption across road, rail, and marine transport.
Ayrton Energy’s electric LOHC system offers a rare combination of:
- High hydrogen density (55 kg-H₂/m³)
- Low temperature, (<100°C), low-pressure operation
- Up to 70% system efficiency
- Compatibility with existing infrastructure
- Safe and environmentally sound handling
In a market where infrastructure costs can derail even the most promising green technologies, we believe our solution stands out as both technically superior and commercially practical.
Hydrogen promises to be a linchpin of global decarbonization, but its potential cannot be realized without a fundamental shift in how it’s stored and moved. By addressing the costliest and most complex barriers to hydrogen adoption, Ayrton Energy is not just optimizing storage—we’re enabling the hydrogen economy.
For industries and governments alike, the message is clear: the time to scale hydrogen is now—and the key lies in smart, scalable infrastructure solutions like this one.