Critical Lessons from Operation Circularity at Mondetta Clothing
The fashion industry generates vast apparel waste annually, with only 1% of used clothing recycled. Mondetta embarked on Operation Circularity in 2021 and is now at the forefront of the sustainable clothing movement. Key steps, including understanding impact, investing in R&D, engaging suppliers for capacity building, and ensuring compliance, traceability, and transparency, are discussed.
Each year, clothing manufacturers produce vast amounts of apparel that never find an end user. For instance, 12% of clothes in women’s wardrobes are inactive, eventually leading to mountains of waste in landfills. As clothes pile up, they release toxins, and the cost of addressing this environmental impact can be as much as 200 euros per pair of jeans. In a world where consumers and companies dispose of 48 million tons of clothes annually, of which a significant percentage ends up in landfills, and only 1% of used clothing is recycled, it is clear that many companies prefer using virgin material over recycled.
On the other hand, the market has changed significantly as consumer demand has shifted towards using more sustainable and eco-friendly products. These changes in consumers’ closets and buying patterns, driven by the growing global awareness of the fashion industry’s massive ecological footprint, are symptoms of the need for significant shifts in apparel industry practices.
The time has arrived to transition to a fabric system that can deliver better environmental, social and economic outcomes – if the apparel industry does not transform now, it will lose the 500 billion USD opportunity associated with changing how clothes are designed, produced, used, and sold. Transitioning to recycled materials is one of the essential solutions for the apparel industry to address its environmental impact. As for each kilogram of recycled polyester fabric produced, compared to virgin polyester, the process uses 99% less water, reduces carbon dioxide emissions by 20%, and utilizes 62% less energy.
“In a world where consumers and companies dispose of 48 million tons of clothes annually, of which a significant percentage ends up in landfills, and only 1% of used clothing is recycled, it is clear that many companies prefer using virgin material over recycled”
Ash Modha
At Mondetta, we recognize the significant impact the apparel industry can have on the environment and know we must do our part and minimize our ecological footprint. Furthermore, genuinely desirable products come from ethical and responsible businesses. We started our journey towards Operation Circularity five years ago, but our supply chain was not ready at that time, and it took us until 2021 get a buy-in and finally start the project to ensure Mondetta takes responsibility for minimizing its ecological footprint and is at the forefront of the sustainable clothing movement. Under this project, we have initiated a radical and massive shift from virgin material to more sustainably preferred and recycled materials.
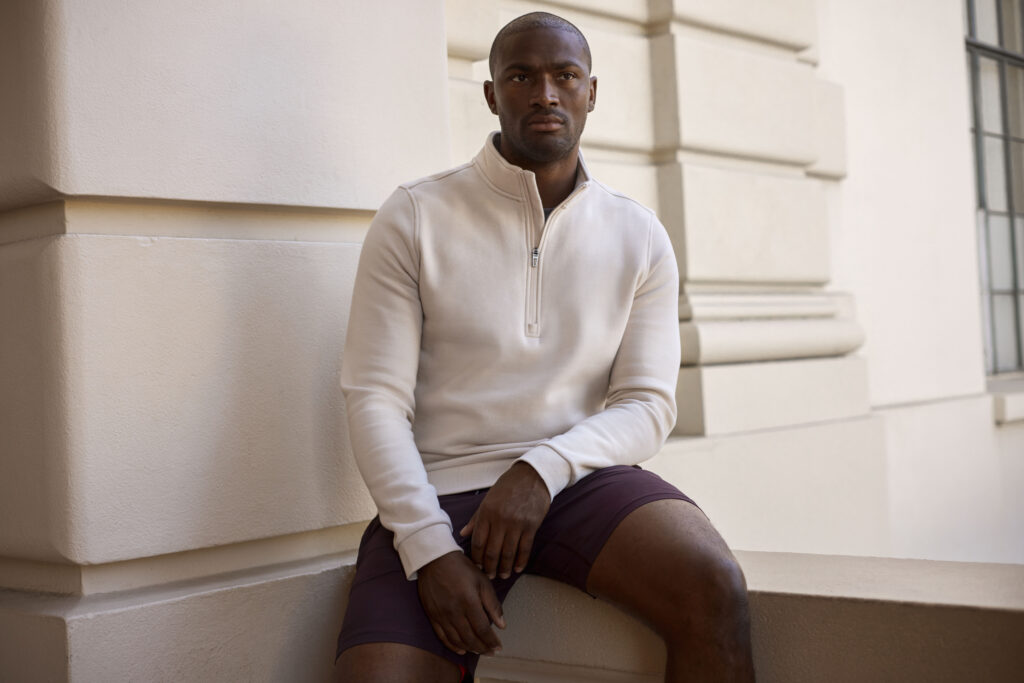
Understanding the impact and setting clear goals – Change comes from within; therefore, it was vital for me to understand the environmental impact of our current practices and inspire the entire team to have that knowledge. Bringing everyone on board has allowed us to co-create and set clear goals and work towards reaching these objectives. Shifting to recycled materials means changing the way we do business, and therefore, getting the team involved was not an afterthought, nor did it require ‘making a pitch’ to get others to sign on to the project at hand; it started top-down, with myself demonstrating the understating of the impact and responsibility to set the course, but was propelled forward by bottom-up engagement from the earliest phases of co-creation and setting clear goals of an initiative through to final execution.
Investment in research and development – When it comes to businesses’ transition to recycled materials, innovation backed up by research plays a pivotal role. Investment in research establishes the proper foundation and resources for corresponding restructuring and implementation of the project with minimum hindrance. For Operation Circularity, we engaged in deep and multi-tiered research before starting the project, the essential elements of which included:
- Reviewing multiple frameworks to work on the organizational recycled materials strategy and related policies.
- Identifying what needs to be restructured in different departments, including the design and supply chain departments, to meet the demands of Operation Circularity.
- Visiting the suppliers, based in different parts of the world, to communicate what we require from them, introduce them to project objectives and bring them on board.
- Researching and establishing the compliance processes to implement operation circularity and the methods to communicate them to the relevant internal and external stakeholders.
Investment in research made the restructuring of systems and implementation a lot easier. Moreover, it is a continuous investment because global practices and standards in the fashion industry keep updating, especially in the face of new and emerging sustainability challenges. Therefore, regular research, updating compliance procedures, and regular communication with stakeholders (internal and external) are necessary.
“When it comes to businesses’ transition to recycled materials, innovation backed up by research plays a pivotal role”
Ash Modha
Engaging suppliers via capacity building – Supplier engagement through capacity building is one of the most critical aspects of transitioning to recycled materials. It is crucial to explain the need for mitigating the environmental impact and corresponding shifts to recycled materials to the suppliers while highlighting the compliance requirements and economic opportunities associated with the transition. Before launching Operation Circularity, we realized that not all suppliers had the resources and infrastructure to produce recycled and sustainable materials, and, in this regard, building suppliers’ capability on the long-term benefits of the shifts helped. We visited our suppliers multiple times to engage them and capacitate them with the need to adapt to our compliance procedures and requirements, including accreditation by the Responsible Down Standard (RDS), Responsible Wool Standard (RWS), and Global Organic Textile Standard (GOTS)/Organic Content Standard (OCS). Doing so ensured that all stakeholders, at every level of the production process, embraced the transition, and the new measures were not just a cursory checkmark for our suppliers.
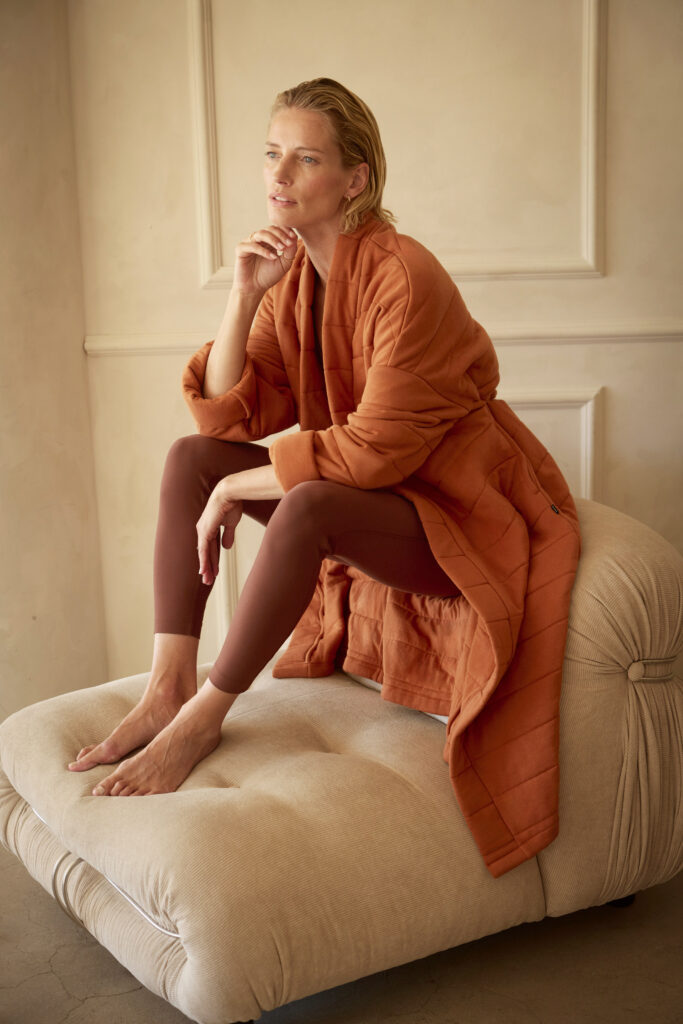
Compliance, Traceability & Transparency – Moving to recycled materials means nothing if we cannot back it up with the appropriate compliance processes, traceability and transparency. Mondetta’s research-based compliance/audit requirements were exceptionally demanding and intense for suppliers, including the certifications required for supplying materials. Therefore, we conducted multiple rounds of meetings with suppliers and prepared corrective action plans for the non-compliant suppliers.
Our supply chain team has worked closely with all our suppliers in 5 countries to promote sustainable practices, including ethical and responsible manufacturing. The fabrics, textiles, and materials we use in our products undergo stringent screenings and checks at every phase of production to ensure our sustainability claims are entirely verifiable. For example, we established a chain of custody and transaction certificate processes to ensure the traceability and verification of recycled content in our products at every step of the production process, from raw material to yarn to the final product.
Additionally, today’s savvy consumers demand visibility into the supply chain and want to know where their clothing comes from and how it was manufactured. Apparel companies can build trust with their customers while showcasing their commitment to sustainability by providing detailed information on compliance procedures, traceability of the manufacturing process, and being transparent about the impact.
Transitioning to recycled materials is a significant step towards contributing to the sustainable fashion economy and is not without challenges. Businesses may face hurdles such as limited availability of good quality recycled materials, reconfiguration of supply chains, stakeholder engagement, and higher production costs. They must remain foresighted, proactive, flexible, and adaptable to confront and overcome these challenges. These competencies will allow businesses to shift to recycled materials by making strategic decisions, organizing required investments, and navigating complications successfully during implementation. This shift represents a solid commitment to a greener future for the apparel industry while making it more resilient.