Li-Cycle Makes an Essential Technology Sustainable
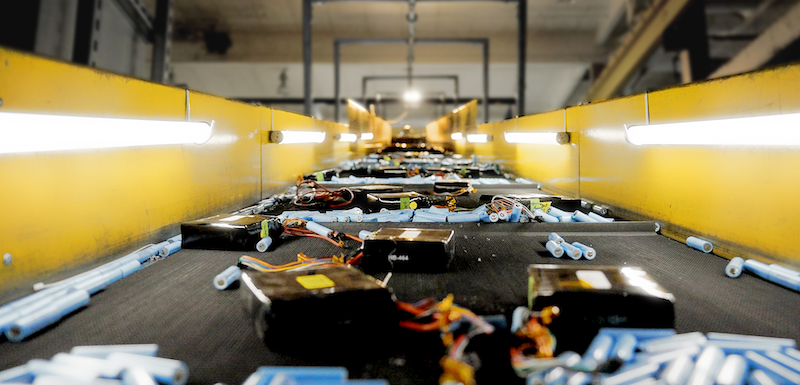
The digital world depends on lithium-ion (Li-ion) batteries, which power a variety of everyday consumer items from smartphones and laptops to wireless power tools. As the go-to energy source for electric vehicles (EVs) and other electrified transportation, Li-ion batteries are a key component of the clean energy future. Manufacturers and engineers commend the batteries for their high energy density and ability to degrade far less over time than traditional nickel-cadmium or nickel-metal-hydride batteries.
However, lithium-ion batteries can create their own set of environmental challenges – but that’s where Li-Cycle’s technology can help. The company has developed a novel, patented process for recycling spent Li-ion batteries and recovering the valuable battery materials within for re-use in new batteries down the road.
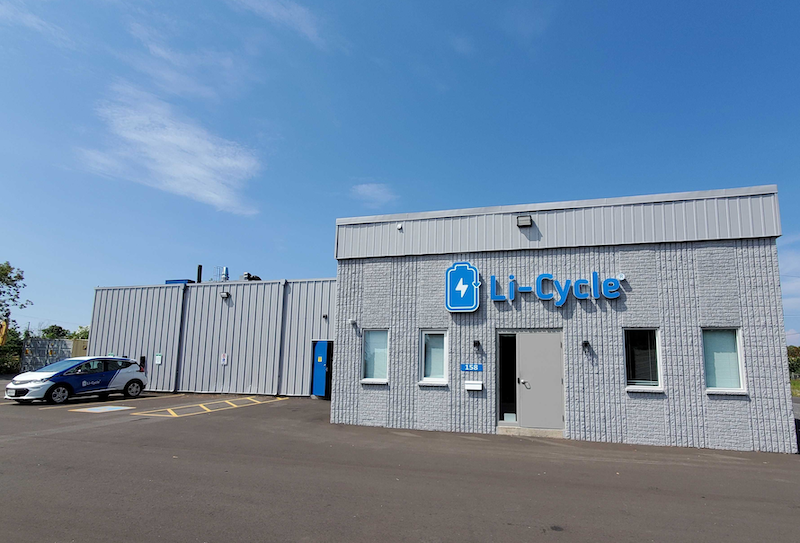
Lithium-ion batteries were first commercialized about 30 years ago. But since 2010, demand for them has climbed by more than 500%. More than 15 million tonnes of Li-ion batteries will reach their end of life by 2030, producing a 2,000% increase in lithium-ion battery waste. The processes required to mine lithium and other necessary battery metals can be even more destructive. These processes can contaminate water supplies and cause air pollution, greenhouse gas emissions, and other forms of ecosystem collapse. Lithium mining also produces significant magnesium and lime waste. Additionally, some of the necessary metals found in Li-on batteries are mined in unstable countries like the Democratic Republic of Congo, where an extraction has been associated with child labour and other human rights abuses, all of which are some of the world’s most pressing issues.
In short, Li-Cycle’s technology will help minimize pollution and greenhouse gas emissions while also helping to provide solutions to human rights abuses associated with producing and disposing of Li-ion battery materials. The company’s goal is to help reduce dependence on mining over time by recycling Li-ion batteries as effectively as possible. While some countries have created recycling requirements for manufacturers and consumers, existing infrastructure generally isn’t capable of recycling all of these batteries. Li-Cycle has developed economically and environmentally sustainable technologies that can recycle any lithium-ion battery into battery-grade chemicals, including lithium, nickel and cobalt. In doing so, the company is returning these resources to a circular economy.
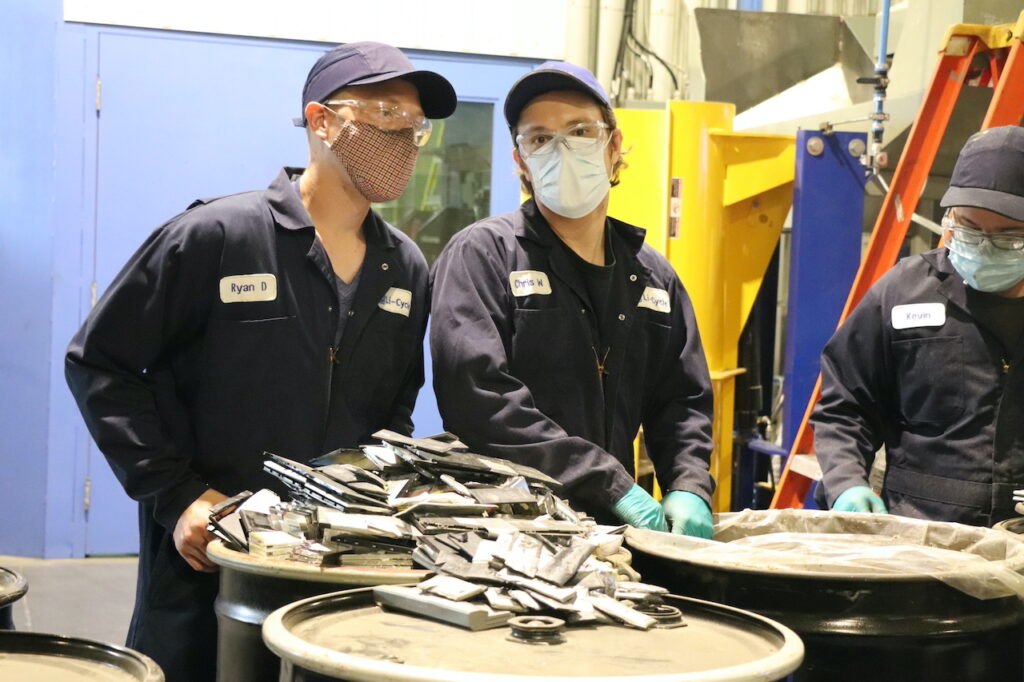
By using a combination of mechanical, safe, size-reduction and specially designed hydrometallurgical resource recovery, Li-Cycle is able to recuperate up to 95% of the materials used in lithium-ion batteries. The materials can then be resold to battery manufacturers. It’s a scalable, sustainable, and safe way to address a messy problem.
Li-Cycle currently operates two commercial mechanical size-reduction “Spoke” facilities in Kingston, Ontario and Rochester, New York, with the capacity to recycle 10,000 tonnes of lithium-ion batteries annually between them. The company recently announced that it is building two more Spokes in North America, one in Arizona and the other in Alabama; both facilities are expected to be operational in 2022. Li-Cycle is also building its first commercial hydrometallurgical “Hub” facility in Rochester, New York. Once complete, it will be the only recycling facility capable of producing all the materials needed to manufacture lithium-ion batteries. As the company expands, it plans to roll out several more Spoke and Hub facilities in Europe and Asia.
In addressing the climate crisis and other forms of environmental degradation, it’s important that the world – and its citizens – do not replace existing forms of pollution with new ones. Some of the planet’s most pressing issues rely on Li-Cycle’s innovation and solutions. The business addresses these issues head-on – and is providing key technologies the world will depend on.