Mehrdad Mahoutian and Carbicrete: The Super-Powered Carbon-Negative Concrete Tech Start-Up Trying to Save the World
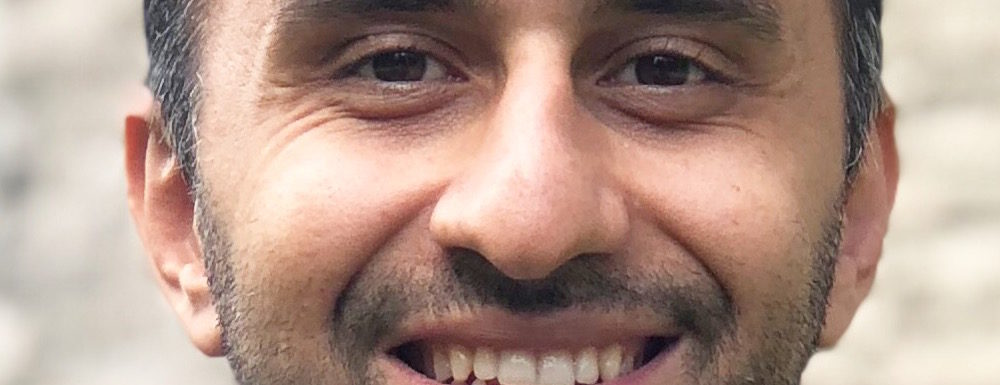
Like many great superhero origin stories, Montreal startup Carbicrete began with something of a happy lab accident. Mehrdad Mahoutian, then a PhD student (2011-2014) at McGill University, and some colleagues were working to to find a, literally, constructive use for CO2. They hoped to identify a by-product or waste material that would react with CO2 in a way that would sequester it and enable the production of construction products. This seemed a more sensible plan than paying a lot of money to store carbon dioxide underground as is the common current arrangement.
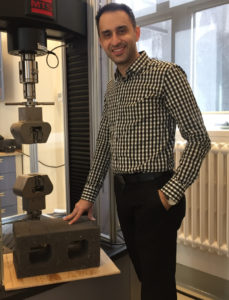
The team tested a variety of materials, but found most of them to be non-reactive with CO2, until they started working with steel slag, a by-product of the steel-making process. Not only was it CO2 reactive, they realized the use of steel slag in construction products resulted in an increase in strength. All rather exciting and then the grinder they were using to grind the slag stopped working properly
Mehrdad sent a chunk of steel slag out to a third-party lab for grinding. What they got back yielded a remarkable discovery; The lab had ground the slag to a much finer size then team ever could ever have done with their own equipment and when they tested their not-in-house slag for CO2 uptake and strength development, they were blown away. They’d found their super power, in steel slag powder.
What Carbicrete’s discovery offers is, essentially, an alternative to the standard method of concrete production that not only doesn’t release CO2, but actually provides carbon sequestration in the process,. They found a way to manufacture cement-free, carbon-negative concrete.
Steel slag both absorb CO2 and gains strength when it reacts with CO2. Adding CO2 to steel slag, and then putting that combination under pressure, forms calcium carbonate, an ingredient found in limestone. Limestone is what traditionally used to make cement, in a highly environmentally taxing process. Indeed, to make Portland cement, the most common type of cement in use, a mixture of limestone and other materials must be heated to between 1,450 and 1,650 degrees Celsius, requiring a large amount of energy and producing CO2 as a byproduct. Carbicrete’s process, avoids producing CO2 and requires no heat, further reducing the net carbon impact of the process.
All of this means that what Carbicrete’s discovery offers is, essentially, an alternative to the standard method of concrete production that not only doesn’t release CO2, but actually provides carbon sequestration in the process,. They found a way to manufacture cement-free, carbon-negative concrete and because this is a by-product meets by-product and make a product arrangement, the costs of production are lower than they are for traditional concrete. The environmental implications of the discovery are staggering, in a good way.
Concrete is the world’s most common building material, the building block of the world as we know it but the production of the cement that has made all that construction possible is highly problematic. It’s very Greenhouse gassy. According to a 2014 study by the Netherlands Environmental Assessment Agency, cement production accounts for as much as 10 per cent of global emissions and most of that cement is concrete bound.
Armed with his new technology, Mehrdad teamed up with Chris Stern, a successful greentech entrepreneur and Carbicrete was founded, with Mehrdad taking the role of Chief Technology Officer. Attention and awards followed quickly. Among them, in spring of 2018 Carbicrete was named one of 10 finalists for the Carbon XPRIZE, a $20 million international competition challenging the world to reimagine what we can do with CO2..in April 2018, it was announced that they were named one of the five finalists competing in a track to convert flue gas from gas plants into CO2. and ultimately use it in a commercial product.
Carbicrete was also named a finalist in Ontario’s Solutions 2030 Challenge, a three-phase competition for innovators to propose solutions that could help Ontario industry reduce greenhouse gas pollution. They received $2.1M from Sustainable Development Technology Canada (SDTC) to help fund a project to optimize elements of its process. Their goal is 100 percent replacement of cement in concrete products and they began by producing full-size concrete masonry units — cinders blocks as they are often called — sans cement.
The company plans to license its patented process to concrete manufacturers worldwide. The carbon tax here in Canada — a tax credit for carbon capture in the United States — will, it is hoped, provide an incentive for customers to make the switch to the cost-effective, carbon-negative construction materials Carbicrete is forging in not-fire.
The struggle may be in finding adopters. As is often the case innovation’s arch nemesis is that villainous duo of Status Quo and his henchman, Complacency. But if we are, literally, going to save the planet, these are characters we all have to guard against .