Business Development Bank of Canada & csr eco solutions: Place Ville Marie Decomission
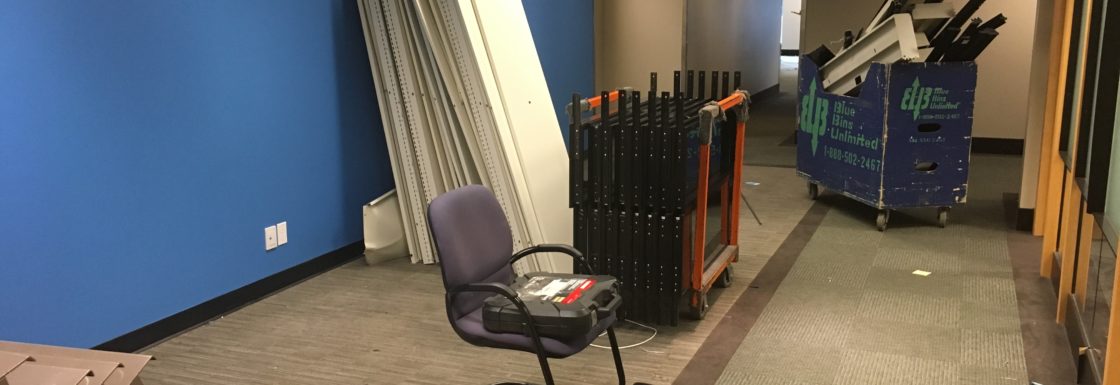
Projects Sponsor
What if we reject the premise that moving means you throw a lot of stuff out, that some kind of literal or figurative pile on the curb is a natural byproduct of transitioning from one building to another?
That’s exactly what The Business Development Bank of Canada (BDC) did when it came time to consolidate their head office, venture capital and Montréal Business Center under one roof at Place Ville Marie. BDC knew that they needed to decommission their obsolete furniture while maintaining operations within existing space. They took this dilemma as an opportunity that led them to consult with CSR Eco Solutions.
CSR Eco Solutions is a global social enterprise dedicated to managing the redistribution of redundant assets on behalf of corporations, government institutions and healthcare facilities. As a social enterprise, their business model has a low overhead that helps to keep the cost of their services competitive with the cost of transporting truckloads of the assets to the dump.
BDC’s overall goal was to have maximum landfill diversion rate, to achieve the highest rate of upcycle for the unneeded furniture, while ensuring maximum monetary return. They collaborated with CSR Eco Solutions who consulted with them on best practice, ideal routes for decommission and what channels benefit others and the planet, all while ensuring financial recovery and thus a plan was made.
The project involved 7.5 floors to be decommissioned at Place Ville Marie along with the venture capital premises location in a separate building. This was realized in 3 phases spanning 2 years. At the completion of each phase, the success of that particular phase was evaluated in order to decide if the direction of recycling versus donation versus liquidation was one BDC wished to continue going down. Then they went on to the next phase.
In the end, over half of the assets were resold and donated, with the remainder being recycled. The recycling was taken to several different facilities, mapping each specific material to a recycling facility to ensure the best environmental practice for recycling.
A stunning 94.16% landfill diversion rate on the project was achieved, amounting to 294.52 tonnes diverted out of the total 312.78 tonnes. A whopping 294.52 Metric tonnes of office furniture and equipment didn’t end up in the landfill, where a less proactive and responsible company might have sent it as just the cost of moving a business, taking the wrong kind of write-off. Of that, 50.03% of the total diverted was resold or donated to charities achieving an auditable 0% landfill rate. The remaining 43.94% was recycled to Best Environmental practice with as little as 5.84% anticipated yield waste.
This is most certainly an idea worth using again.