Creating Compostable Plant Based Plastics
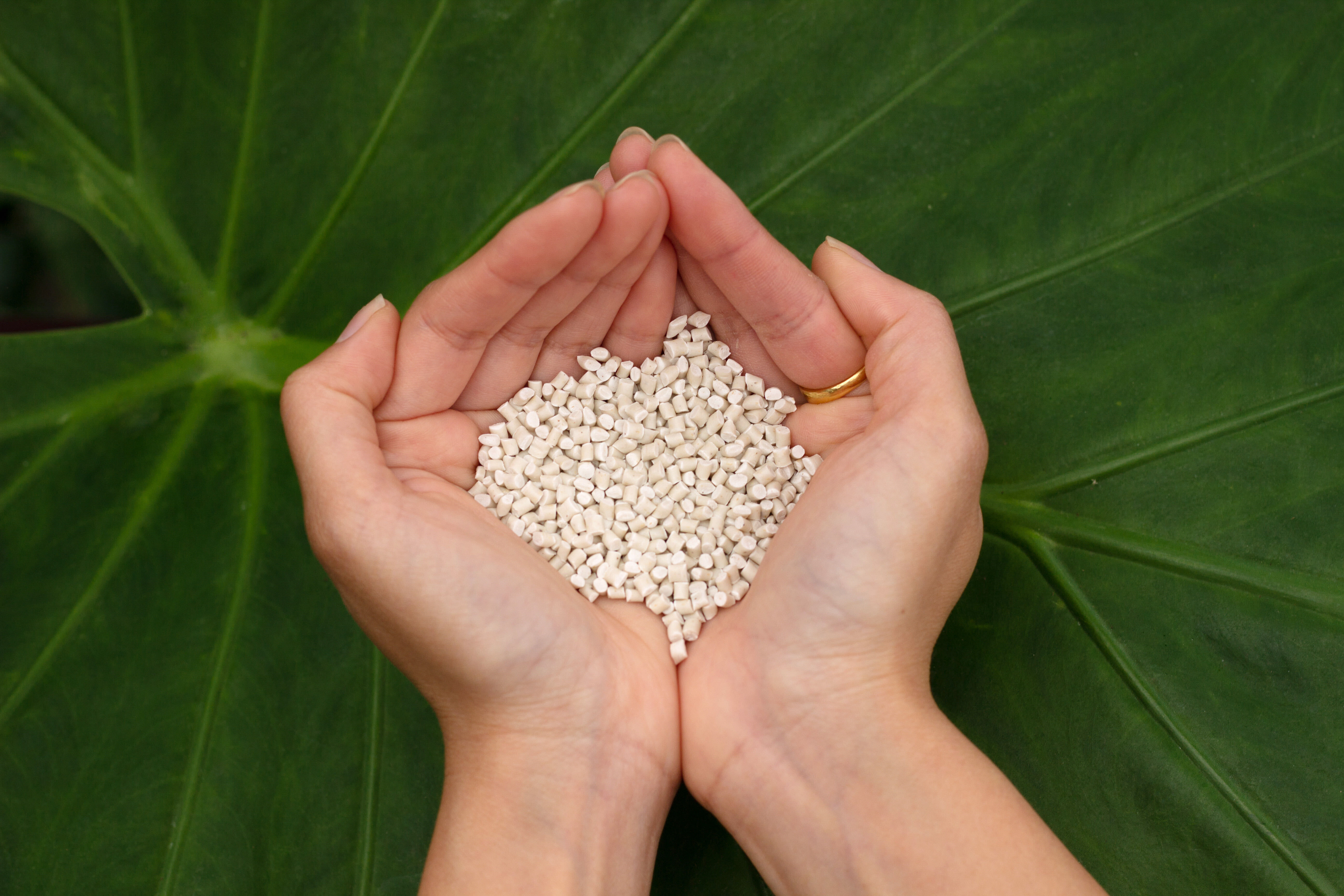
Projects Sponsor
Back in 2019, start-up erthos Inc. was determined to help tackle the global plastic waste crisis and developed the first prototype of their plant-powered resin/materials. At the same time, they were building relationships with plastic manufacturers globally because that was the connection that they wanted to make.
The erthos advantage is that not only are their materials significantly greener and more circular than their plastic counterparts, they are compatible with existing plastic technology, meaning they fit seamlessly into pre-existing supply chains.
With this technology in hand, erthos began a consumer-packaged goods pilot with AB InBev’s 100+ Accelerator from which they developed the world’s first plant-powered keg cap.
From the get-go, erthos understood that tackling the global plastic waste crisis as their mandate––working with plastic manufacturers and consumer brands was vital to scaling their plant-powered packaging impact. The erthos team knew that launching an ambitious global pilot required a solid foundation and committed partners. They also knew that if their consumer-packaged goods pilot was to be successful, it needed to have a framework that integrated sustainability within core business priorities.
That key compatibility was found with AB InBev’s 100+ Accelerator.
The pilot’s objectives were clearly defined to prioritize what was most important for both parties. They wanted to create a plant-based alternative to an existing plastic product with measurable environmental benefits and verify compatibility with AB InBev’s manufacturing partners through iterative trials. Brainstorming ways to replace existing single-use plastics with AB InBev’s 100+ Accelerator team, the erthos team collaborated with AB InBev’s product and research teams to a rather surprising end.
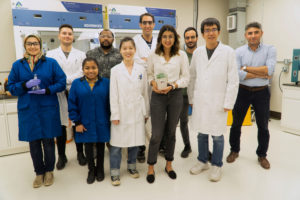
While the end goal was to develop potential resin solutions addressing different problematic plastics in consumer-facing streams, they soon discovered an application within their internal supply chain that had never been on anyone’s radar: the keg cap.
The keg cap, a plastic product, with its limited or even single-use application, compatibility, and lack of existing sustainable alternatives, fits all of the project’s initial targets. Keg caps may be small, but they equate to almost 1300 tonnes of global plastic consumption. Wanting to make a plant-based mountain out of that plastic mountain, erthos worked closely with AB InBev’s manufacturing team to understand the exact mechanical, thermal, and technical requirements for the caps, and that work paid off.
Remarkably, erthos managed to integrate substantial sustainability metrics into the final product. By developing a resin that was not only a 1-for-1 replacement to their existing polypropylene resins, but was also compostable, biobased, and entirely non-toxic, thus, food contact safe. They created the world’s first plant-powered keg cap, but not overnight.
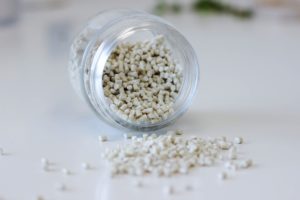
As with every new technology, the path to development was riddled with barriers, obstacles, and challenges, and their development process was no different. Biobased, biogenic materials such as the ones employed by erthos, are notoriously difficult to work with. They are more prone to burning at the higher temperatures required to process plastics and dissolve when in contact with water. For an application such as a keg cap, which is being developed in India, the material needed to be one that was not only able to withstand the wear and tear of the production process but also demonstrated stability during transport and storage, etc., especially when in contact with liquids.
In initial pilot runs, erthos’ material was prone to melting through the equipment moulds due to incompatibility with higher temperatures, and the high moisture content in the surrounding environment. As a result, one of the significant challenges of developing this resin was understanding the trade-off between developing a material with higher barrier properties and relative hydrophobicity to impart stability, when in high humidity conditions. Meanwhile, it doesn’t compromise on composability, which relies primarily on hydrolysis reactions. This was one of the significant challenges that faced the team. It required major pivots in their formulations and updates to our technology platform. Yet, through determination and innovation, obstacles were overcome and their ground-breaking keg sealing plant-powered cap was born.
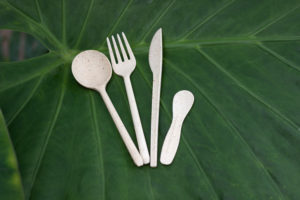
Keg caps made with erthos’ resins have significant water, energy, and CO2 savings when compared to their traditional plastic counterparts, and that’s just the beginning. Building on that success, erthos is currently in the process of scaling up this resin’s production process and is now working with major consumer packaged goods brands and manufacturers to replace other rigid, single-use plastics.
They are also working with industry leaders, and sit on boards, councils, and committees that govern the development of compostable plastics, and the industry at large. You have to tip your cap to their cap and watch to see what they do next.