GreenQ Partners: Refrigeration Optimization
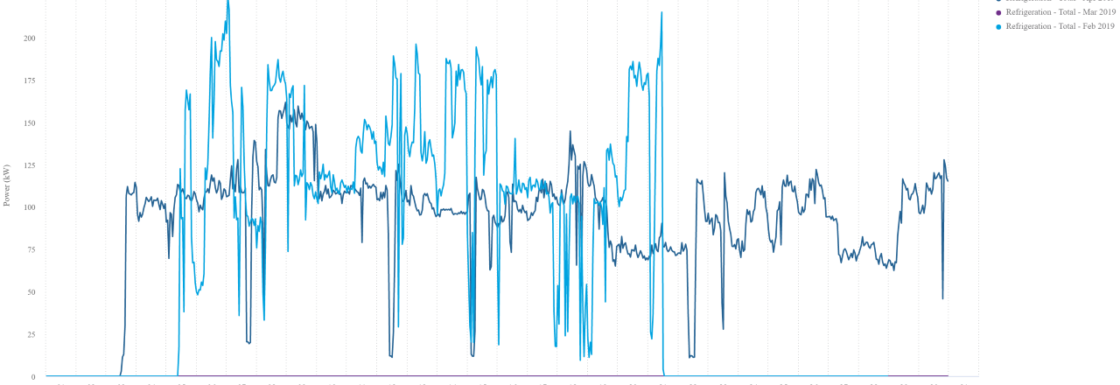
Projects Sponsor
Stone cold savings; GreenQ Partners find chilling efficiencies in a warming world
Refrigeration plants are typically one of the biggest electricity consumers at food manufacturing facilities. They are a highly complex system able to meet a consistent cooling load while working under different settings and operational procedures.
In a way, operating an industrial refrigeration plant is not unlike driving a car; one can get from A to B using very different amounts of gasoline. Yet historically very little thought has been given to the “mileage” of a refrigeration plants.
Most industrial refrigeration plants are set up to meet cooling/freezing loads without consideration for minimal consumption of electricity. Anyone pressing for an in depth energy audit of an industrial refrigeration plant would likely have been told “Just chill,” but the team at GreenQ Partners is turning that around.
GreenQ Partners are dedicated to providing their clients with goal-oriented, transparent energy management that boosts the client’s competitiveness by saving them money. They set out to identify, establish and validate the most energy efficient operational procedures and settings possible for the particular production and storage requirements.
Their refrigeration system optimization specialist, Sergei Khoudiashov has been working in the area of industrial refrigeration for more than 20 years and has presented on the topic of refrigeration system optimization at European and American conferences. The client could trust that Sergei was going to give them more than “Don’t stand there with the door open” and they weren’t disappointed.
The GreenQ Partners team created a consumption baseline by recording the directly measured consumption of the whole plant – including all fans and pumps – over two weeks. In accordance with Measurement and Verification standard (IPMVP) they built a baseline that accounted for production load and ambient weather. With the plant under energy consumption monitoring, they were able to identify operational deficiencies and instruct maintenance team on how to correct them. They also identified opportunities to change equipment settings to reduce energy consumption while still meeting the cooling load.
Mechanical and electrical contractors had GreenQ Partners’ expert guidance, installing VFD controls for condenser fans. Then, as a final step, the team validated the savings achieved through comparison between actual consumption and baseline forecast.
Because GreenQ Partners’ optimization technics are not common knowledge within the industry, a certain amount of education, one could say ice-breaking, is involved in this kind of process. Plant staff have to be given time and information in order to feel comfortable about plant’s ability to meet cooling and freezing loads
Similarly, the mechanical and electrical contractors—both contractors on the job gravitated towards traditional, less energy efficient operational procedures—needed to be educated about the project’s steps. All part of the job for GreenQ Partners whose work has extended the expected life of the plants compressors—the most expensive part of the refrigeration plant—by reducing their load and run time.
Several pieces of failed equipment were also identified during the project, failures that had gone unnoticed in winter that would have limited cooling capacity of the plant in summer, requiring rush repairs — but that’s not even the big story here.
The big story here is that project reduced annual consumption at the plant by an estimated 374MWh (33%) and that’s very good for the planet as well as the plant. With payback for the project under 2 years, GreenQ Partners is proving that savings are a dish best served cold.