SEMECS Varennes Anaerobic Digestion Project: Greenfield Global
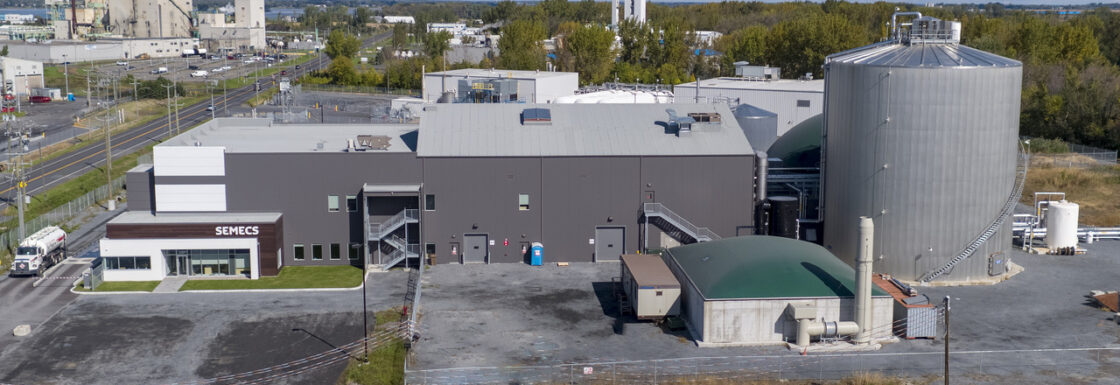
Projects Sponsor
In order to reduce greenhouse gases, Quebec is banning organic waste in landfills. Greenfield Global developed an anaerobic digestion project with three regional municipalities to divert 40,000 MT of organic waste per year to produce biogas and biofertilizer. The biogas is then used by Greenfield’s ethanol plant across the road to offset 4 million cubic meters of natural gas per year. The fertilizer is used by farmers replacing 10k MT of chemical fertilizers. This is a first-in-kind project in North America.
Greenfield Global’s vision can be summed up in three digits and a less than sign: “<350.” If healthy human life is to be sustained on earth, the amount of carbon dioxide in the atmosphere must be reduced to less than 350 ppm and Greenfield is commit to making that possible.
Greenfield operates one of the largest ethanol plants in Canada in Varennes, Quebec – turning corn into 200 million liters of biofuel per year. Ethanol production uses natural gas to dry distillers’ grains that are sold as an animal feed. The company’s objectives are to reduce the amount of that fossil fuel required in this process while helping regional municipalities in Quebec divert tens of thousands of tonnes of organics from landfills.
Organics that decompose in landfills are a leading contributor to climate change; releasing methane and CO2 (the most harmful greenhouse gases) into the atmosphere as they break down. To combat emissions the province of Quebec is banning organics in landfills.
By turning organic waste into valuable products like biogas and biofertilizer, Greenfield both provides a solution to the challenges posed by the ban and reduces the carbon footprint of their ethanol plant. At the same time, a way for farmers to reduce their carbon footprint for corn production through the use of a bio-fertilizer is opened up.
Getting there wasn’t straightforward. In part because there were many stakeholders, but also because every anaerobic digestion (“AD”) project has its own unique set of circumstances. Considerable research was required in many areas.
Understanding the composition of the feedstock in the regional municipalities was crucial as the type of waste being processed dictates the technology and process required to digest the feedstock.
Greenfield researched the composition of the feedstock over several seasons and evaluated all of the available technologies at an industrial scale. The team traveled to Europe (leaders in AD) 6 times over 2 years to evaluate technology providers and visit operational AD plants. The results were the need for a “Wet Pulper” technology for Quebec’s type of waste stream, and BTA (a German AD technology provider) was selected.
It was important to ensure that the digistate (the co-product produced after the biogas is stripped from the waste stream) could be used by farmers as a substitute for chemical fertilizers. The planting acreage and environmental certificate requirements to allow for the digestate to be used as a practical substitute for fossil fuel fertilizers had to be evaluated. The results were that the digestate is a perfect substitute for other fertilizers, and there are plenty of willing customers for the biofertilizer.
Research into the use of biogas as a substitute for Greenfield’s natural gas use in its process was also undertaken. Biogas from the AD plant would have a different density than fossil fuel natural gas. How would the biogas be scrubbed? What changes would be required in Greenfield’s process to accept the biogas? What happens if the AD plant has a shutdown? What are the economics between biogas and natural gas now and in the future?
The results were significant modifications to Greenfield’s incoming gas train, and a long-term agreement with SEMEC––a company dedicated to assembling PCBs on an industrial scale––for the biogas.
With that partnership was formed, and the waste stream was secured, the conceptual engineering commenced to define the scope of the project, as well as the defining the capital and operational expenditures for the AD plant.
A business plan used to seek grants and financial support for the project was put together and a parcel of industrial zoned land across the street from our Varennes ethanol plant was purchased. This is ideal for bringing garbage trucks in, digestate out, and the biogas across the road to the ethanol plant, via a short pipeline.
Up and running Greenfield is now diverting 40,000 metric tonnes of organics from landfill each year and displacing 4 million cubic meters (12%) of their natural gas consumption at their Varennes ethanol plant with clean, green biogas. They’re replacing 10,000 metric tonnes of chemical-derived fertilizer with biofertilizer from their digest from the plant, which in turn is being put on fields to grow more corn for the ethanol plant.
This impact will increase threefold with Greenfield’s expansion to 120,000 tonnes at the end of 2021. Not just in Canada, but North America wide, the SEMECS project is demonstrating the circular economy in motion and bringing <350 a little closer.