Resilient modular system; strong enough for hurricane zones but adaptable for all climates
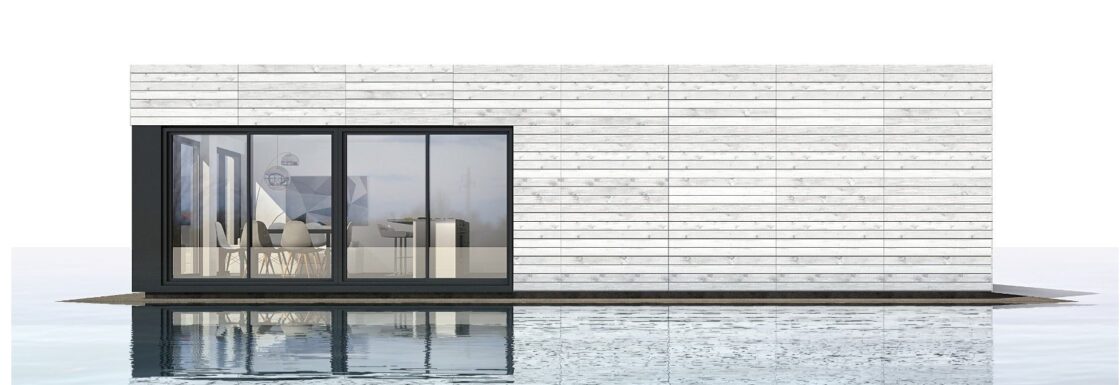
Casa Duro is a resilient modular building system that brings together the conjoined benefits of modular and prefabrication all in one package. In a thoughtful approach emphasizing multifaceted flexibility, it is also assembled rapidly on-site. This patent-pending technology addresses the need for streamlined building and durable resistance to extreme weather caused by climate change.
The construction industry is wrought with many inefficiencies, according to Patricia Russell, CEO of Casa Duro Inc. and the primary designer of the Casa Duro system.
“[The inefficiencies] may be due to the complexity of bringing together several different professional disciplines and skills together in one solution. However, the more urgent issue compounding this problem is extreme weather patterns caused by climate change that are so strong that typical construction isn’t resilient or durable enough anymore.”
Patricia Russell, 2021
For decades now, we’ve been hearing about the environment being in trouble, but concerted action has been slow. Climate change has been proven to increase the occurrence and strength of extreme weather such as floods and hurricanes with such alarming results; it’s finally getting the attention of governments and investors worldwide to be viewed as a problem for which solutions are required.
We can see slow changes in our own country to adopt appropriate measures to mitigate climate change. The Canadian government has mandated that every new building be net-zero energy ready by 2032.
Further south, the devastation caused by extreme weather as of late has resulted in the IMF stepping in and insisting that new builds must meet resilient standards in the Caribbean. This has had an effect on underwriter’s insurance policies and thus an effect on financing approval for real estate developments.
In Mexico, the federal government has already halted developments that do not meet sustainability standards.
Investors managing assets worth $32 trillion have called on governments and businesses to step up efforts to tackle climate change, like HSBC, Nomura Asset Management, and UBS Asset Management.
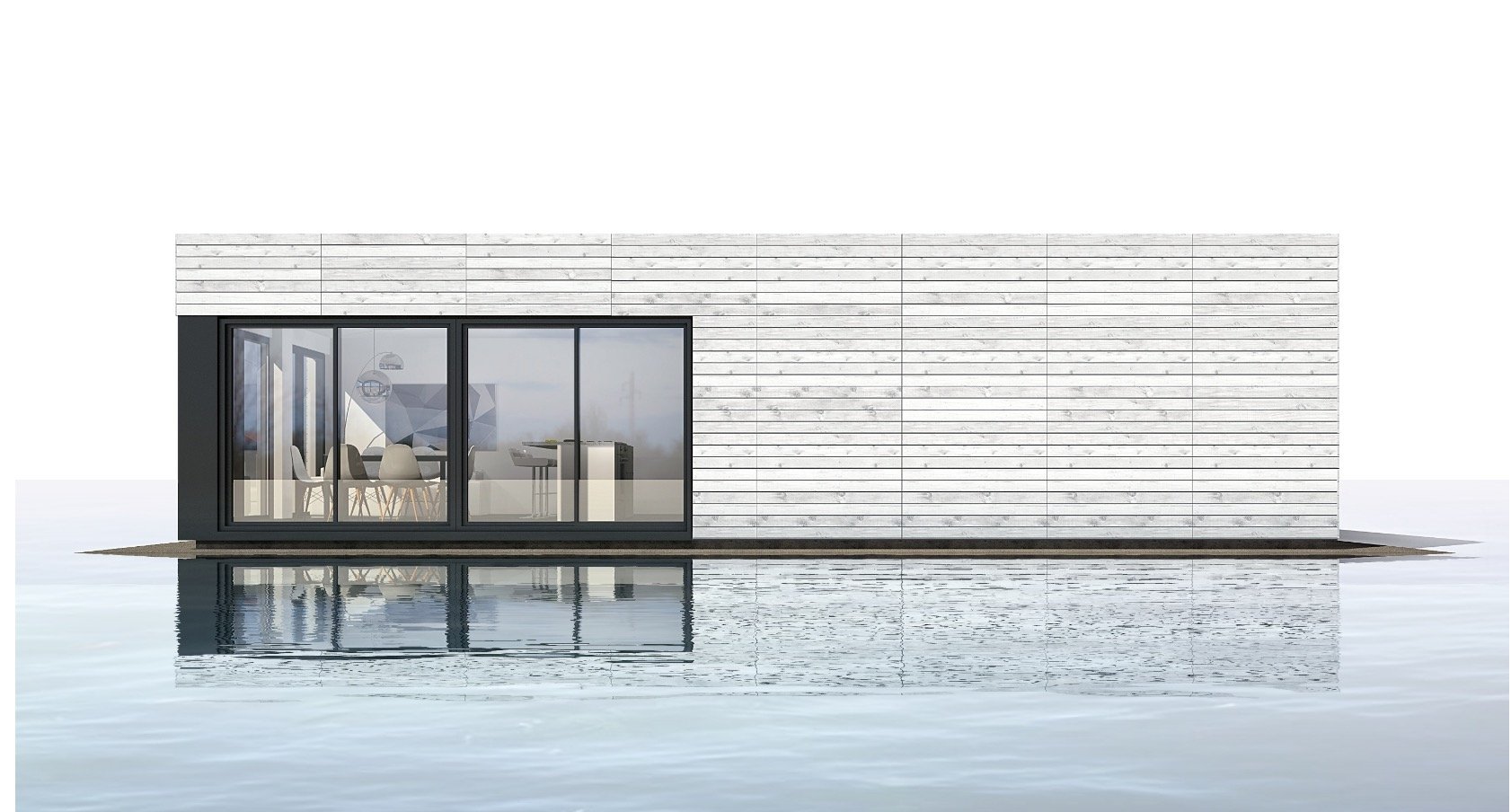
The problem that Casa Duro fixes through its innovative approach is rooted in the need for improvements in construction, specifically related to onsite inefficiencies, construction material waste, the longevity of the product and extreme weather due to climate change. At the final stages of R&D, with a launch date of Spring 2022, Casa Duro is positioning itself to be a uniquely qualified company to solve the building problem faced by those seeking resilient dwelling technology and or a more sustainably optimized approach to prefab and modular.
The Casa Duro System comprises three simple sub-systems: Structural modules, Exterior Walls and Interior Wall Systems with The Control Panel.
Casa Duro’s structural modules allow for a variety of configurations or designs from single-storey to multi-storey buildings. The ridged design of the modules allows for flexibility of interior layout to accommodate designer and clients’ tastes.
The Exterior Wall System has been designed to be extremely tough to resist hurricane-force winds up to 225 mph if required and is also compatible with a wide variety of material finishes.
The prefabricated wall sections arrive at the site and are installed rapidly.
The outer wall sections are strong enough to resist extreme weather and in the case of projectiles, the modular sections are designed such that damage can be easily fixed without jeopardizing the energy efficiency or waterproof benefits of the second line of defence walls which maintain comfort levels adaptable for all climates.
The Interior Dismountable Wall System arrives fully prefabricated with plumbing and electrical already installed. Wall sections arrive and plug into special receptacles. The finish material of the interior walls has a unique feature that allows for the removal of the finishes with multiple purposes in mind. One benefit of the removal feature is the lifecycle of the wall structure, which can be saved when upgrading the finish material during renovations or during maintenance or upgrading. The ability to remove a material section of a wall undamaged and replace it reduces downtime during renovation, maintenance, upgrades in smart home technology and allows for the recycling or resale of the unwanted finished material.
The Interior Dismountable Wall system also includes a control panel that houses all of the control elements of the home and can be seen as the brains or central operations of the building, such as electrical, computational, mechanical, and HVAC. Operational control hardware housed in the control panels communicates with other dismountable walls. The number of control panels depends on the size of the building and is distributed in zones. The control panel(s) is also equipped with the same flexibility of removal of finishes which allows for ease of access and upgrades at any time.
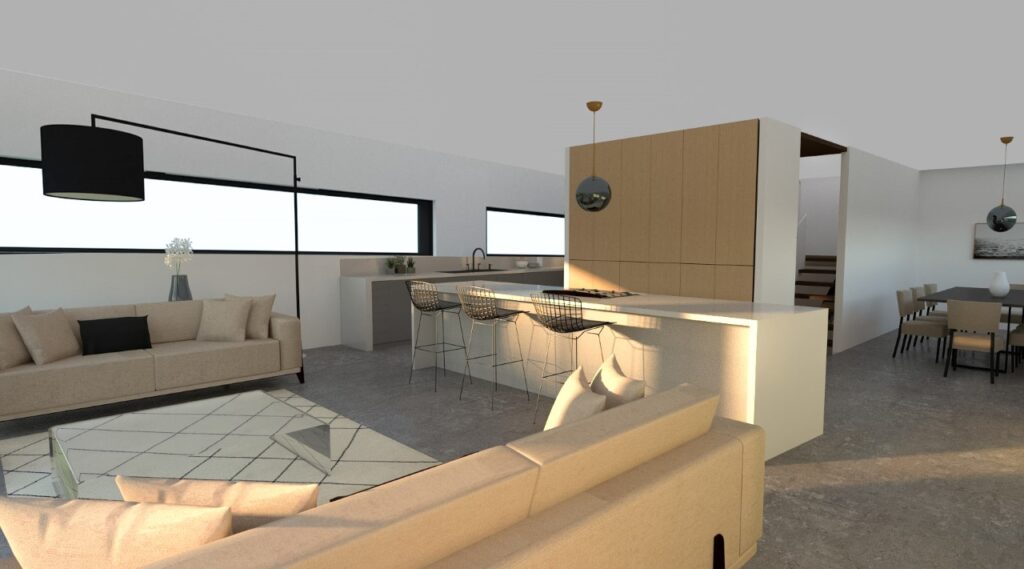
In addition to architectural education, Patricia also trained as an energy auditor with the National Research Council of Canada. Early in her career, she used her training and education to start working independently executing redesign and renovation projects.
“I definitely didn’t command the authority on-site, nor was I taken seriously,” Patricia recalls being under the impression that the workers didn’t realize that she knew about or understood the building science and process thoroughly. “I can recall on one particular occasion; I felt the quality of the work was at risk because of lack of attention to energy efficiency and a few other building issues and I was able to halt the project. With the approval of the client and with the help of another skilled craftsperson and two subcontractors, we finished the project together slowly but successfully. This project made me realize that it’s just too easy for a project to go badly within the unsystematized methods of traditional construction. Details in a project rarely come together as they were intended on-site within traditional construction and this often means the abandonment of energy efficiency or sustainability practices”.
In the construction industry, a building detail may not be realized in actuality as the architect or engineer may have designed it initially. Each building detail in itself has numerous variations depending on the designer and the result can change beyond what was initially designed depending on who is building it. There can be 4-5 people involved in a building detail. The architect may not have the experience that the builder has, nor will the builder have the same understanding as the architect or the engineer.
“Bringing together three or four different disciplines and finding one solution is not easy. I believe that this is why innovation in building construction happens slowly,” she said, “I felt there was a need for a solution that brought together the various disciplinary perspectives and the whole building process re-organized, re-designed, and reimagined to be more sustainable and that’s why Casa Duro exists.”
She said the idea of Casa Dura evolved through her observations and seeing a need.
“Through being involved in renovations, I often felt the pangs of guilt each time I saw the amount of construction waste that was being carried away,” she reflected. Often the material could have been saved with a little bit of careful planning but she knew her popularity on-site would suffer if she interrupted or asked for alternative careful techniques to preserve the material. She also knew that everyone involved in the project would not want to adapt, because it would slow down the project and ultimately be a waste of time and money. An easy-to-use innovative system was needed to reduce the amount of waste and so she started to design solutions.
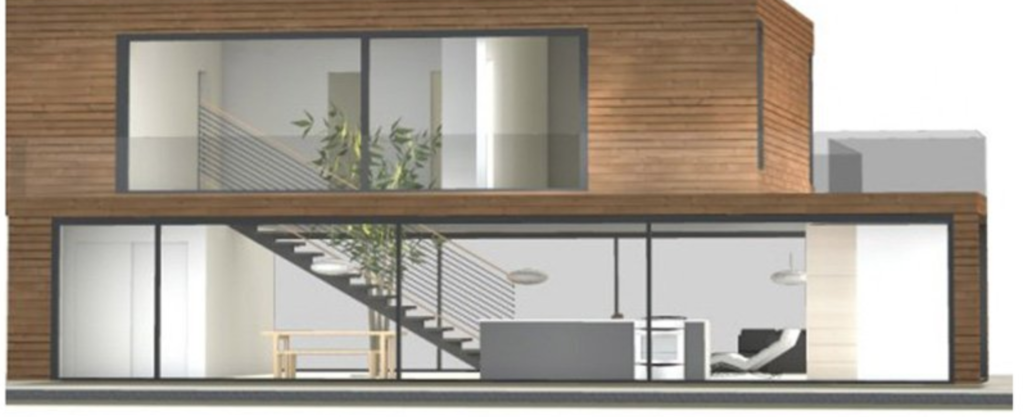
Now, through innovation of interior wall systems, Casa Duro is making it easier to preserve and recycle unwanted or outdated finish materials that would otherwise go to the landfill by engineering the core walls to be more durable and an attachment system that allows for the interchangeability of finish materials. The same applies to exterior walls with respect to mitigating waste from possible damage caused by storms, for our exterior cladding system. The energy efficiency and resistance to flooding are always kept intact if there is damage to the exterior wall, due to the separation of purpose being brute strength for the first line of defense walls and the inner’s optimal energy efficiency performance.
Currently, there are few other options for residential applications or for the real estate or hospitality industry that offers a finishing system that doesn’t look industrial, or a system that allows for effective upgrading without long downtime, debris, and unnecessary wasted material. Reusing structural frame material of the wall is easy, because there is no damage when removing the finish material.
When asked why she engineered her building system to resist winds of 225mph, she stated, “Have you seen the devastation throughout the Caribbean, up along the Eastern seaboard of The US and Atlantic Canada? The decimation of buildings is not just happening in the Caribbean anymore. It’s happening in Ontario, Quebec, Newfoundland, and other Canadian provinces. We need to prepare for these weather patterns to intensify and upgrade our building standards.”
If we needed proof of climate change driving impacts up, Hurricane Ida hit Louisiana last week with sustained winds of 150 MPH, and gusts to 175 MPH. To help put that in context, “Category 4”, 150 MPH storms, such as Ida, are a staggering 250 times more damaging than a category 1 hurricane. Downtown New Orleans clocked winds over 90 MPH. At 150 MPH, a piece of debris coming at you would travel the length of a Canadian football field (330 feet) in exactly 1.5 seconds.