Sustainable lithium refining for a greener battery-value chain
The growing market for electric vehicles means less transportation emissions, but their batteries contribute their own set of GHG emissions. Saad Dara, Clean50 honouree and CEO of Mangrove Lithium, explains how sustainable lithium refining practices and technologies can be utilized to lower the footprint of EV batteries.
The importance of the energy transition from fossil fuels to renewables becomes more important as global climate change becomes more imminent and dire. In no sector has the world seen greater adoption of this philosophy than in the automotive industry. Electric vehicle (EV) sales are growing exponentially, and even surpassing sales of some types traditional internal combustion engine (ICE) vehicles in parts of the world.
Although this is a promising marker for reducing global greenhouse gas (GHG) emissions and quelling climate change, EV’s come with their own set of contributions to GHG emissions and climate change – in no small part due to the reliance on lithium required in EV batteries. However, with more sustainable lithium refining practices and technologies, the carbon footprint of the EV battery value chain can be substantially reduced, making the environmental impact of EVs more in line with their intended purpose.
A dirty secret behind the ‘green’ narrative of EVs is that they contribute to more GHG emissions than their fossil fuel counterparts at kilometre 0, before they even reach the hands of the consumer. As outlined in this Harvard Gazette article, materials needed for EV production generate a sort of carbon overhead that takes 28,069 to 68,160 miles to equal the total GHG emissions of ICE vehicles and start netting any emissions benefits. Simply put, EVs are dirtier to make but cleaner to drive. Current methods of lithium refining to a battery grade lithium hydroxide or carbonate for cathode manufacturing is a net contributor to this carbon overhead that exists in EV manufacturing.
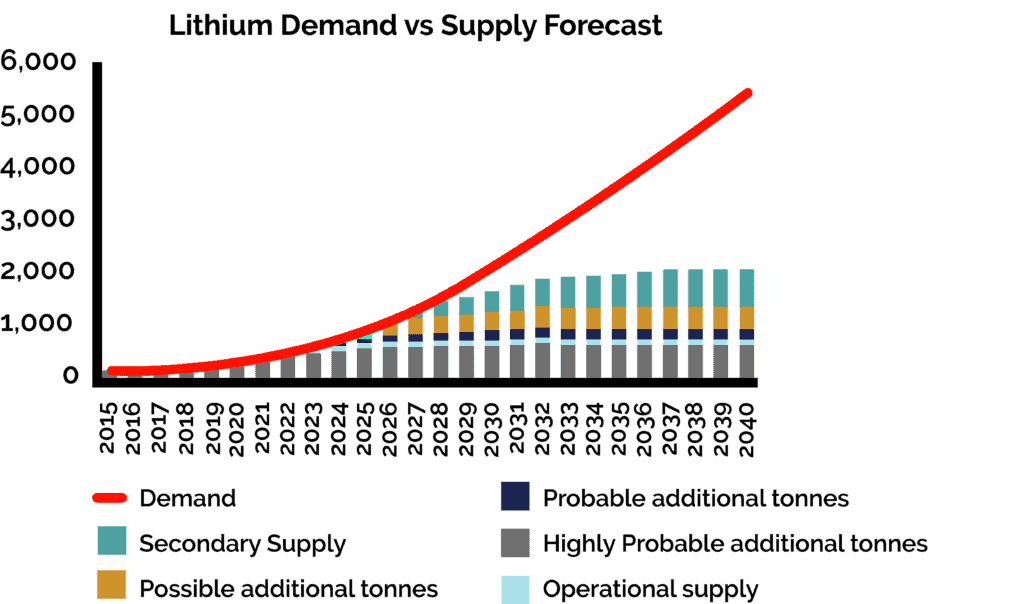
There is much to be made about the environmental implications of upstream mining and extraction of raw lithium, as well as downstream giga factories and battery manufacturing; however, the missing middle that needs greater consideration is the refining process that converts raw lithium into a battery grade product. The refining stage has significant implications for not only the availability of lithium but also its sustainability. This is primarily due to 4 main factors: where lithium is being refined, the waste by-products produced in the process, the technology being used to refine it, and the source of the lithium feedstock.
Lithium is a globally produced commodity with majority of extraction coming from hard rock mines in Australia, or brines in South America. Other reserves and operations exist in North America, Europe and Africa. Despite this, majority of all the extracted lithium is transported to China to be refined into lithium hydroxide and carbonate for batteries. This extra milage between lithium extraction and lithium refining, and subsequently to battery manufacturing, adds a significant carbon footprint to the battery-value chain.
The environmental regulatory practices in China further add to the ecological impact of the current state of lithium refining. Chinese lithium refining has been halted in the past due to waste pollution spilling into waterways. Having domestic lithium refining operations would not only cut down the transportation miles of the lithium supply chain, but it would also ensure that it would be held to the scrutiny of local environmental protection laws and standards. Domestic lithium refining would also open supply chain bottlenecks by mitigating geopolitical risks and logistical issues that currently exist.
There is another elephant in the room when it comes to the sustainability of lithium batteries. Currently, the world’s largest lithium production operations are hard rock assets in Australia, where lithium sulfate is processed from spodumene, which is then refined into battery-grade lithium hydroxide and carbonate. During the refining process from lithium sulfate to lithium hydroxide, using incumbent technologies, a large amount of sodium sulfate waste by-product is produced. For every ton on lithium hydroxide made, 2 to 2.5 tons of sodium sulfate waste is also made; and with the sodium sulfate market saturated, the ‘room’ will soon entirely ‘elephant’ if the waste is not disposed of or treated. This disposal carries additional costs and energy expenditure.
Mangrove’s electrochemical technology can either refine the lithium directly creating no waste by-products or convert the waste sodium sulfate back into the chemicals required for lithium processing – eliminating any burden of disposal that exists in current refining processes. This reduces cost and energy expenditure and helps boost the overall sustainability of the battery-value chain.
The next factor mentioned impacting lithium sustainability is the core technology and methodology being used to refine extracted assets into a battery-grade lithium. Incumbent processes rely on chemical and energy intensive phase separation processes to convert lithium sulfate and lithium chloride into lithium hydroxide. This process essentially requires chemicals to drive the transformation from one lithium chemical compound to another. Such processes result in significant GHG emissions associated with the production and logistics of the chemicals, potentially release mineralized carbon dioxide into the atmosphere during the battery making process, and often introduce impurities resulting in poor yields or further processing.
An electrochemical process, such as Mangrove’s, utilizes electricity in place of chemicals to drive the refining process, which improves yields and purity while being a more sustainable process even when natural gas based electricity is used. Furthermore, in countries such as Canada, electrochemical systems will be able to exploit the readily available renewable hydroelectric power, compounding the technology’s sustainability.
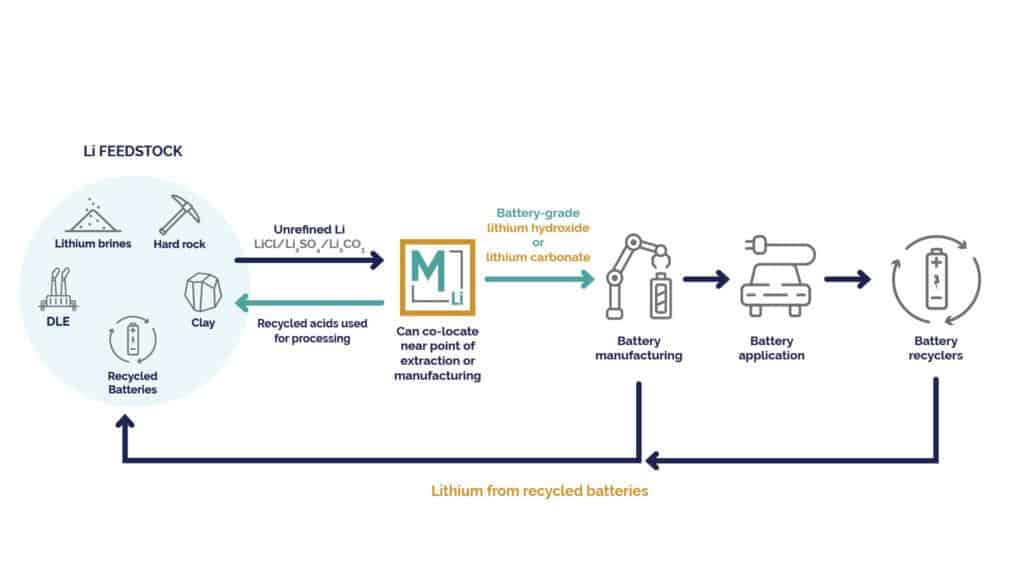
The last of the four main factors affecting the sustainability of the lithium refining system is the feedstock flexibility of incumbent technologies. Traditionally, lithium has been extracted from naturally sourced assets, such as brines or hard rocks; however, just as all natural resources are, lithium is a finite asset that has limited availability in nature. As the growth for renewable energy continues, the more lithium will be extracted from the earth, diminishing supplies of natural reserves. The ability to effectively refine lithium from recycled batteries will be paramount if the lithium supply chain is to be sustainable.
Mangrove’s electrochemical refining technology can convert lithium extracted from recycled battery black mass into a high purity battery-grade product without the introduction of additional chemicals and with relatively low energy expenditure – creating a fully electrified sustainable circular economy between lithium processing, refining, battery manufacturing and battery recycling. This is all achieved without the creation of any waste by-products that must be treated or disposed of. This ensures an ever-present availability of lithium, helping to keep the disparity between lithium supply and demand as tight as possible.
The transition to renewable energy and the adoption of EV’s isn’t a magic bullet solution to lowering GHG emissions and eliminating climate change. As with all other lines of production, refining lithium for batteries comes at an environmental cost. However, measures can be taken to mitigate the environmental impact of lithium production, such as enabling domestic refining and using electrochemical technology to convert raw feedstocks into a battery grade product. This will in turn not only help create energy security and to stabilize the lithium supply chain, but it will ensure refining is as energy efficient and environmentally sustainable as possible – reducing the carbon overhead of new EVs.