The PVD Approach – a More Sustainable Way to Advance Battery Technology for a Greener Planet
The lithium-ion battery has revolutionized the electric vehicle sector, significantly reducing greenhouse gas emissions. Overcoming concerns about battery metal scarcity, innovations like Li-Metal’s Physical Vapour Deposition technology show promise in producing cost-effective, environmentally friendly lithium metal anodes, supporting the growth of a cleaner EV industry.
Since it was introduced commercially in 1991 by Sony and Ashai Kasei, it’s become universally accepted that the lithium-ion battery is a breakthrough discovery redefining the way we store energy. The electric vehicle (EV) revolution is fundamentally changing the way we move around, and is only the first fleeting sign of the monumental impact electrification will have on all aspects of our lives. The positive impact these batteries have had on our climate is tremendous, as an EV produces less than 60-68% greenhouse gas emissions over its lifetime compared to a gas-powered car. These benefits will be magnified when advanced battery powered applications such as electric aircraft become commercialized. However, for that to happen we need battery technology to advance.
There are many promising new battery technologies and several are focused on replacing graphite in the battery anode – one of the two electrodes that make up a battery cell. Graphite as a material presents its own set of environmental challenges, including very high carbon dioxide emissions associated with its production, and next-generation battery technologies, generally, are attempting to replace graphite with a better material to increase energy density while reducing weight and volume for optimal performance and cost. However, most roads lead to ultra-thin lithium metal anodes, which have the highest specific energy capacity of all anode materials with 10x capacity compared to traditional graphite anodes.
Once widely commercialized, batteries with lithium metal anodes can be highly cost-effective and result in dramatic improvements to the volume, weight, and range of EV batteries compared to today’s lithium-ion batteries. With lithium metal anodes, batteries can either have the same amount of charge in a smaller battery, or an improved level of charge with no change in the size. Lighter, cheaper, and more powerful batteries are key enablers of future EVs and electric aviation. With lithium metal anodes, we could have EVs on the road that are able to travel 1000 kilometres on a single charge as soon as 2030, overcoming the range anxiety that many would-be EV buyers in Canada face today.
The Importance of a Better Battery Supply Chain
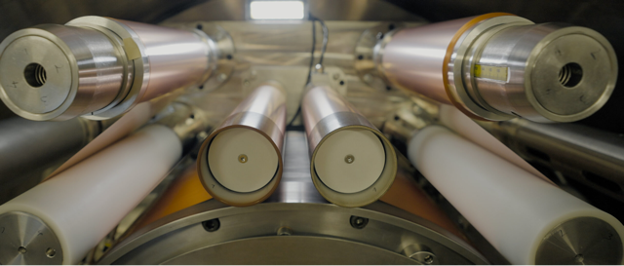
There is a prevailing view that a major problem with the battery supply chain is that battery metals are running out – this is slightly misguided. Short-term scarcity caused by rapid growth of the industry is not indicative of the general abundance. When thinking about long term viability, we should focus on lithium, because this is the most difficult material to substitute in truly high-energy density batteries. The USGS estimates a total world resource of about 90 million tonnes of lithium in 2023. For perspective, that’s enough for more than 10 billion EVs, without considering recycling or alternative sources – we’re not about to run out any time soon, but extraction and processing capacity is needed in North America to support growth.
“When thinking about long term viability, we should focus on lithium, because this is the most difficult material to substitute in truly high-energy density batteries”
Maciej Jastrzebski
Aside from lithium, there are more legitimate concerns around high-performance cathode metals, as these are both scarcer and their extraction has been linked to environmental and human rights abuses. These metals, namely nickel and cobalt, can be substituted by other more prevalent materials. Substitution becomes much more attractive when lower-performing cathodes are paired with high-energy density anodes, where a big boost in performance comes from completely eliminating the graphite anode and replacing it with lithium metal, allowing materials like iron phosphate to be used.
The Traditional Problem with Producing Lithium Metal Anode Materials
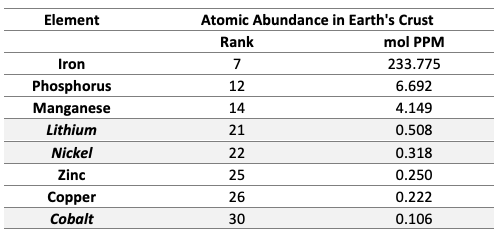
Switching to iron-phosphate or iron-manganese-phosphate cathodes can
eliminate the need for the more difficult cathode metals.
To help increase the penetration of EVs, the next-generation battery industry is focused on attaining cost and performance parity with internal combustion engines (ICEs). Currently, the cost of today’s battery is a significant component of the overall cost of the EV and the industry is targeting battery costs of $100/kwh or less. However, the cost of lithium metal makes the use of anything but the thinnest lithium anodes more expensive making adoption harder.
A core challenge with the prevailing method for producing lithium metal anodes today, is that it’s not suited to producing ultra-thin anodes in the wide formats needed for EV batteries – a key requirement to achieving cost targets and scale. Furthermore, this inherently leads to excess lithium content in the batteries, contributing to increased risk of a fire, impacting safety, and is also highly wasteful because of the considerable environmental cost of mining and transforming lithium ore into metal.
In the medium term, building out capacity to process lithium salts into metal is the most likely bottleneck for next-generation batteries. More than 90% of existing processing plants for lithium metal are based in China and rely on high-purity lithium chloride; a precursor material for which only limited production capacity exists, and which produces 5 tonnes of toxic chlorine gas per tonne of lithium metal produced. This has negative environmental consequences, and through more complex permitting, promises to be a drag on the roll-out of lithium metal production capacity.
Turning to Physical Vapour Deposition
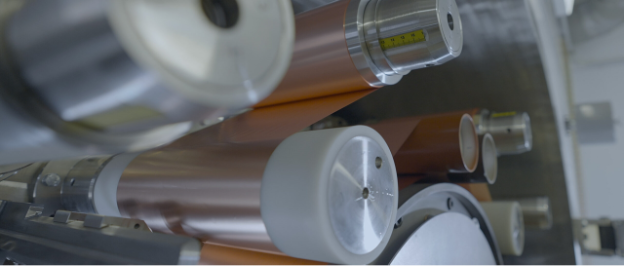
Physical vapour deposition, or PVD, as a technology platform, dates back to vacuum experiments carried out by Michael Faraday in 1857, but did not find widespread commercial application until the middle of the 20th century.
Since then, PVD processes have been producing millions of square metres of low-cost materials per year, ranging from low-cost metallized food packaging materials to high-tech optical and semi-conductor coatings. Anything that looks metallic, but is made of plastic, is likely to have been made from PVD. The ubiquitous example of a PVD product is the shiny metallic coating inside of a bag of potato chips.
PVD’s unique capabilities and flexibility in producing consistent, ultra-thin films makes it the ideal technology for producing battery anodes. It’s an environmentally friendly technology with clean processes that involve minimal hazardous materials, and avoid generating chemical waste or water pollution. For anode production, it can ensure that just the right amount of lithium is used for optimal battery performance, while limiting waste.
Building the Future on the Li-Ion Battery Foundation
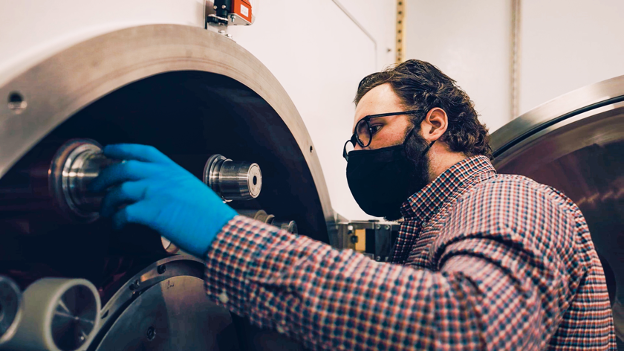
equipment to produce anode materials for next-generation
batteries.
At Li-Metal we have been pioneering a vertically integrated metal and anode production platform that uses PVD to produce lithium metal anodes, and a novel lithium metal production process to supply the raw material. Rather than using extrusion; squeezing, flattening or pressing a piece of lithium metal down to the required thickness; we build it up by using PVD to deposit lithium metal directly onto substrates from the bottom up. We minimize the amount of lithium metal used in our process, which reduces waste, improves safety, and eliminates the need for graphite.
To support our PVD technology, we have developed a modular, environmentally friendly, chlorine-free process that uses ubiquitous lithium carbonate salts, commonly employed as the lithium source in lithium-ion batteries, as its feedstock. We believe we were the first company in the world to produce lithium metal directly from lithium carbonate, and we were proud to accomplish this in Canada.
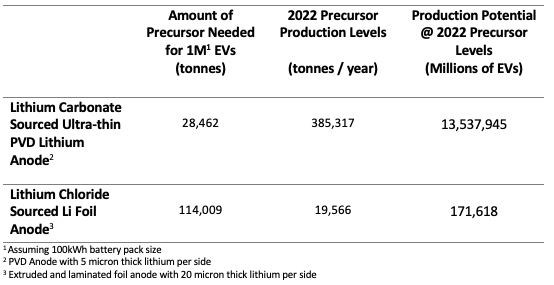
Ultra-thin anodes using lithium carbonate feedstock can support 100x more vehicles.
By minimizing the quantity of lithium metal used in each battery, our PVD technology will help with resource intensity while further enabling the substitution of cathode metals, such as cobalt and nickel. Our novel lithium metal production process will help enable the development of a cleaner, domestic lithium metal supply chain as next-generation battery manufacturing scales to support EV adoption in North America.
The potential of leveraging PVD for battery materials and its environmental impact has been underestimated. It can solve some of the inherent challenges in making lithium metal anodes perform well in batteries to help make the case much easier for a consumer to choose an EV over an ICE.